Ca++
Well-known member
I think they are the baby of the group, if keeping with this style. Today it's £6 delivered (<$10) but 12v (standard stuff)
Solenoids, if you need them, are about £4 in this size
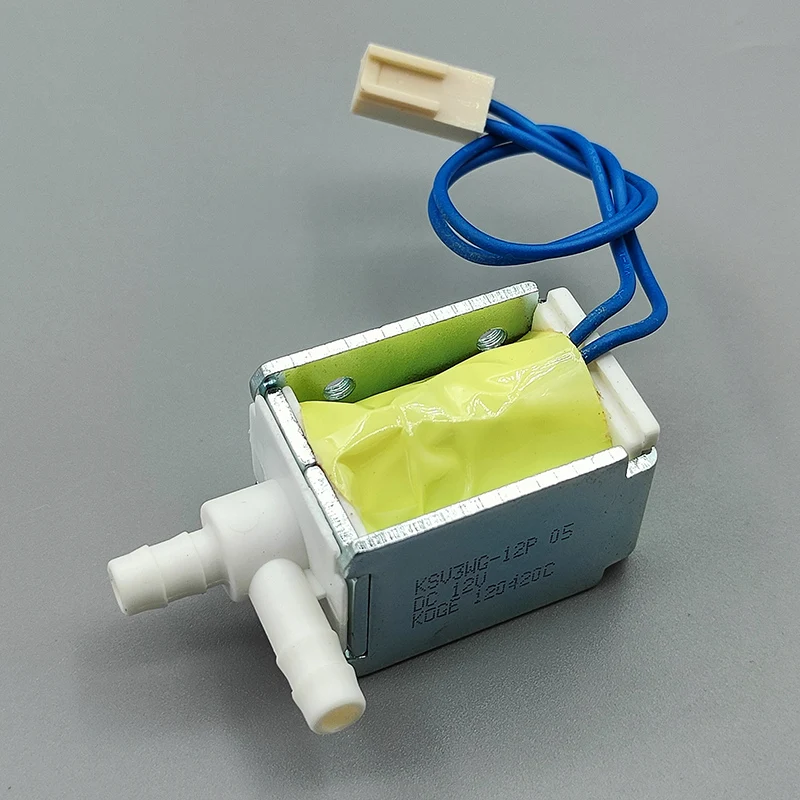
2.11C$ |DC 12V 2 Way Mini Electric Solenoid Valve Normally Closed Small Air Vacuum Water Switch Flow Control Valve DIY| | - AliExpress
Smarter Shopping, Better Living! Aliexpress.com
12v timer, for your 12v system, maybe £7.50