littleone
Member
Hash Press (small, stainless) made from a Turn Buckle and Spirit Pourer.
(Be warned that this project may be very difficult/imposable, expensive and a waste of time.
It is posted for your entertainment or consideration)!
Components:
The main component is a Stainless Steel Cable Adjuster used in boating; it might be called a Turn Buckle? You will notice I have replaced one of the threaded end bolts with another of longer thread.
For the Press Tube seen to the right of the Turn Buckle I cut a piece of Stainless Tube from a Spirit Pourer for Spirit Bottles.
From the end of the Spirit Pourer I cut the tapered piece off and used it on the end of the thread to help with its guidance down the Press Tube.
Live it, Spirit Pourer and Jigger available in home wares sections.
On the far right labeled “BOLT” are the final components needed for functionality; Bung and Piston followed by an optional 3rd piece.
(Machining a Stainless Steel Bolt down accurately was challenging and cost me 2 of my 3 bolts before achieving high tolerance pieces that I was pleased with).
Bolt Machining Process:
It was achieved by putting the length of Stainless bolt in an Electric drill. (Cut the Bolts Head of first).
I then laid the drill horizontally on a desk with the protruding bolt spinning like in a lathe arrangement.
Then I used the Angle Grinder or Friction Cutter at around 45 degrees angle to the bolt working along a section until it is close to the required size, finishing is done with a stone.
The drill and wheel should be working against each other, spinning in opposite directions.
(The stone is slower but better than removing too much material, take it steady).
The”Working Drill against Wheel Technique” can also be used to face the ends.
Using the flat side of the grinding or cutting wheel squarely against the spinning bolt end, a square and smooth finish is possible.
A high degree of skill and patients is required and if you lose an eye or finger stupidity may also be included. The new fine cutting wheels are good for cutting the lengths (if you must, be careful).
Warning and considerations:
I do not suggest anybody should go to the bother of assembling this equipment or use electrical tools as I have, actually if not potentially this is dangerous.
For most the premade equipment is the way to go, for others this example maybe the trigger for your solution using materials that are available to you.
Availability of bushes and other small engineering components could be helpful.
Cheers Littleone
(Be warned that this project may be very difficult/imposable, expensive and a waste of time.
It is posted for your entertainment or consideration)!
Components:
The main component is a Stainless Steel Cable Adjuster used in boating; it might be called a Turn Buckle? You will notice I have replaced one of the threaded end bolts with another of longer thread.
For the Press Tube seen to the right of the Turn Buckle I cut a piece of Stainless Tube from a Spirit Pourer for Spirit Bottles.
From the end of the Spirit Pourer I cut the tapered piece off and used it on the end of the thread to help with its guidance down the Press Tube.
Live it, Spirit Pourer and Jigger available in home wares sections.
On the far right labeled “BOLT” are the final components needed for functionality; Bung and Piston followed by an optional 3rd piece.
(Machining a Stainless Steel Bolt down accurately was challenging and cost me 2 of my 3 bolts before achieving high tolerance pieces that I was pleased with).

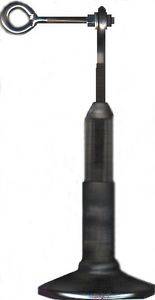
Bolt Machining Process:
It was achieved by putting the length of Stainless bolt in an Electric drill. (Cut the Bolts Head of first).
I then laid the drill horizontally on a desk with the protruding bolt spinning like in a lathe arrangement.
Then I used the Angle Grinder or Friction Cutter at around 45 degrees angle to the bolt working along a section until it is close to the required size, finishing is done with a stone.
The drill and wheel should be working against each other, spinning in opposite directions.
(The stone is slower but better than removing too much material, take it steady).
The”Working Drill against Wheel Technique” can also be used to face the ends.
Using the flat side of the grinding or cutting wheel squarely against the spinning bolt end, a square and smooth finish is possible.
A high degree of skill and patients is required and if you lose an eye or finger stupidity may also be included. The new fine cutting wheels are good for cutting the lengths (if you must, be careful).
Warning and considerations:
I do not suggest anybody should go to the bother of assembling this equipment or use electrical tools as I have, actually if not potentially this is dangerous.
For most the premade equipment is the way to go, for others this example maybe the trigger for your solution using materials that are available to you.
Availability of bushes and other small engineering components could be helpful.
Cheers Littleone